Finding the right cleanroom door for GMP pharmaceuticals can be a challenging task. Cleanroom doors are vital for protecting the integrity of pharmaceutical and food items and contribute to overall operational efficiency.
Pharmaceutical industries have various options when it comes to cleanroom door accessories. Accessories include:
- hardware
- style
- flush
- frame
- door leaf
- material
- maintenance requirements
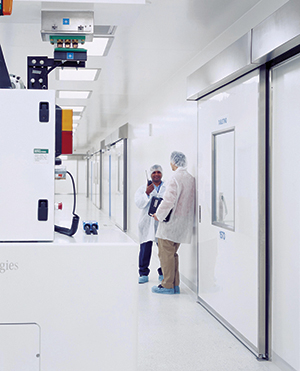
Pharma Sliding Door
Ultimately, you want a cleanroom door designed to be easy to clean, has a durable core and frame and is high performance.
Traditionally, pharma doors consisted of various materials, such as laminate, wood, fiberglass, and steel. However, GMP door regulations now prohibit wooden doors. This limitation is because wooden doors fail to provide adequate temperature regulation and require extensive cleaning and maintenance. As a result, pharmaceutical companies prefer to use fiberglass or stainless-steel doors.
Pharmaceutical cleanroom doors, buyers have several factors to consider during purchase, including hardware, compliance, and more. Below is a comprehensive guide on what to look for when choosing a cleanroom door.
What to Look for in a Pharma Door and Door Frame
Manufacturers design cleanroom doors to help protect pharmaceutical products by preventing contact with contaminants in various areas. Anyone in the pharmaceutical industry understands the unique challenges of meeting different codes and requirements while maintaining easy access to and from pharmaceutical items.
A high-quality cleanroom door allows for easy opening and closing while still protecting the sensitive pharmaceutical items inside the room. With hundreds of options, it can seem challenging to discern which door is best for your pharmaceutical cleanroom. Below are some essential hardware characteristics that a cleanroom door should have to ensure optimum protection for your pharmaceutical products.
The Door Is Compliant
One of the most vital factors to consider when shopping for cleanroom doors is whether the doors meet compliance regulations.
The pharmaceutical industry has the unique responsibility of meeting several codes and compliance regulations to ensure product quality. These regulations come from several authoritative groups, including:
The regulations for door types set by these associations will vary depending on the industry. For example, companies that use their cleanrooms to store food will need to meet different codes than those that store pharmaceutical items.
Cleanroom doors must also meet GMP hardware regulations when housing pharmaceuticals. To meet GMP regulations, the doors must be designed with a seamless surface and frame, be unable to carry bacteria, and will not warp when in contact with disinfectants.
A cleanroom door must meet the required regulations and codes to perform all necessary functions adequately. A pharma door is designed to protect pharmaceutical items and employees. These doors also safeguard the quality of items delivered to customers and help pharmacies avoid various legal issues.
The Door Maintains Proper Levels of Humidity
Cleanroom doors play a critical role in maintaining humidity levels. Generally, cleanroom guidelines require the room’s relative humidity, or RH, to stay between 30 and 40% throughout the year. These days, every well-designed pharma door comes with a high-quality flush, surface, and other hardware to control relative humidity levels according to specific regulations.
Inadequate humidity levels can cause more than an uncomfortable work environment. When the relative humidity levels fail to meet the required percentage, it increases the chance of bacterial contact and corrosion. As a result, pharmaceuticals, and food can become damaged, have a shorter shelf life, and have lower overall quality.
Additionally, fluctuating humidity levels can lead to static electricity, which impacts how the particles in the cleanroom move around.
Aside from product damage and degradation, inadequate humidity levels can create an uncomfortable work environment, reducing overall efficiency and leading to more operational mistakes. Therefore, when looking for a pharma door, check that it has the necessary hardware, flush, surface, and frames to maintain adequate humidity levels.
The Door Regulates Temperatures
Quality cleanroom doors will maintain sufficient temperatures even with constant opening and closing. Minor temperature changes can dramatically impact the quality of food and pharmaceutical items, putting customer satisfaction and safety at risk.
Generally, cleanrooms should remain at 69.8 degrees Fahrenheit (21 degrees Celsius). Cleanroom doors should maintain this temperature while allowing easy access to and from the room.
Various factors can contribute to cleanroom temperature changes, such as the cleaning schedule, employee accessibility, and in some cases, customers. If the temperature is too low, individuals with access to the room can shiver and affect particle movement. If the room is too warm, technicians and employees can start to sweat, which will impact the quality of the pharmaceutical or food items in the room.
Essentially, a cleanroom door should allow easy access to and from the room while maintaining adequate temperatures to protect the integrity of the items inside. The door leaf, frames, surface, and flush are different factors contributing to a cleanroom door’s ability to regulate appropriate temperatures.
The Cleanroom Door Has a Strong Seal and Flush
Having a full-sized seal is vital for a cleanroom door’s ability to regulate humidity, temperature, and bacteria contact prevention. Not all cleanroom areas have the same door frame or entry, so it is essential to find a cleanroom door that fits the unique structure of your cleanroom while still providing durable seams and effective sealing.
It is also critical that the flush and sealing of the door be flexible yet durable. Some seals and door seams can make opening or closing a door difficult, affecting overall productivity and product accessibility. However, cleanroom doors must also have a certain level of durability to effectively keep out contaminants and maintain adequate temperatures Relative Humidity levels.
The Door Has Fast Opening and Closing Rates
The longer you leave a door open, the greater the chance of unwanted contaminants and moisture entering the cleanroom. Therefore, a cleanroom door should protect the quality of the pharmaceutical and food items and allow easy and fast access in and out of the room.
Slow opening and closing rates increase the chance of air incursion and contaminant entry. It can also make it difficult for employees or customers to access the contents inside. The flush, surface, and weight of a door can affect how easy it is to open and close.
When searching for cleanroom doors, ensure the door quickly opens and closes easily. However, don’t sacrifice durability or overall quality for a door with faster opening and closing rates.
The Cleanroom Door Maintains Effective Pressurization
Adequate pressurization of a cleanroom is easy to overlook. However, improper pressurization levels can affect the quality of pharmaceutical items.
High-performance cleanroom doors are designed to maintain effective pressurization within the room. This prevents cross-contamination. When looking for cleanroom doors, check the frames, surface, core, ledges, and flush to ensure that they can maintain proper pressurization levels and effectively protect your pharmaceutical items.
The Door Makes for Easy Cleaning
The frames, ledges, flush, and material of a cleanroom door can affect how easy it is to clean. Keeping the cleanroom door free of bacteria and contaminants is vital to prevent cross-contamination, bacterial growth, and pharmaceutical or food degradation.
Using corrosion-resistant materials, are designed to simplify and accelerate the cleaning process. All components of wash-down doors must be completely cleanable, and they must be durable enough to withstand water and cleaning agents on a frequent basis.
Cleaning the door is an essential part of overall maintenance. How often you should sanitize the door will ultimately depend on your industry and how you use the door.
Why Are Cleanroom Doors Essential?
Cleanroom doors have the vital task of protecting pharmaceutical items while contributing to employees’ overall efficiency and work experience. Choosing a door requires more than picking out a
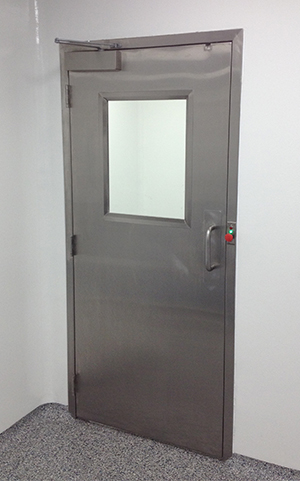
Stainless Steel Pharma Door
favorable style. A door frame, flush, surface, and material all contribute to how well your room can protect the integrity of the pharmaceutical items.
Investing in a high-quality and easy to clean door can help you reduce costs by:
- Extending the life of pharmacy and food items
- Improving employee efficiency
- Reducing maintenance expenses
- And more
Preferable cleanroom doors are also replaceable and easy to use.
In Summation
To summarize, there are several different factors to consider when it comes to choosing a pharma door:
- Frame and flush quality
- Ease of maintenance
- Surface material
- Style
- Door hardware
- Temperature and humidity regulation
It is also essential to consider how replaceable the door is. Should an accident happen that severely damages the door, it is vital to replace it as soon as possible. Unfortunately, replacing a broken door often requires a temporary operational shut-down, impacting overall efficiency and delivered product quality.
Finding doors that can meet various legal regulations, require minimal maintenance, and have a durable surface is a guaranteed way to protect cleanroom contents and boost productivity.
For more information or to find the perfect door for your needs, don’t hesitate to get in touch with our ASI Doors team today at (800) 558-7068. sales@asidoors.com